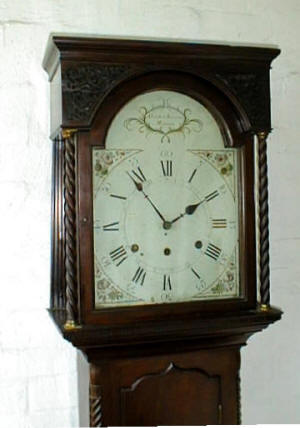 |
The
clock to be restored in this section is an unusual Scottish longcase, c.
1800. The maker, Quentin Jamieson of Maybole is not listed in the
standard texts, however the website of the town of Maybole in Scotland
mentions this maker, having been born in 1772.
At
first glance, the clock appears to be a 3-train longcase, which would
normally indicate a clock chiming on bells, however it is more
interesting and possibly rarer than that. The right 'winding hole' you
can see on the dial is actually a dummy to balance the other two holes -
the left for the strike and the centre for the time. What completes the
puzzle is what's missing from the clock before restoration - the centre
seconds hand and the centre date hand. |
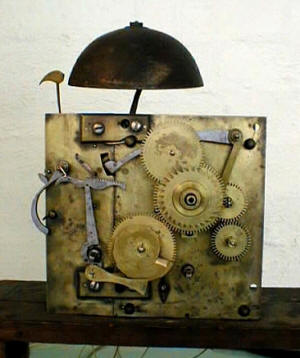 |
This is
the first look at the movement after removing the dial, revealing the
unusual features of this clock. You can see two straps towards the left.
These 'strap' a separate strike mechanism to the central time mechanism.
Once these are removed, the strike section comes away, almost like an
optional extra. The three large wheels you can see (from the top) are
the date pusher wheel (driven with a 1:2 reduction from the 12-hour
wheel below it), the 12-hour wheel with the date wheel concentrically
mounted on top of it, and the snail wheel, driven directly from the
12-hour wheel.
The
reason for the layout being in this manner may be that the maker made
more of the centre seconds timepiece clocks, but decided later to add a
striking version to his catalogue |
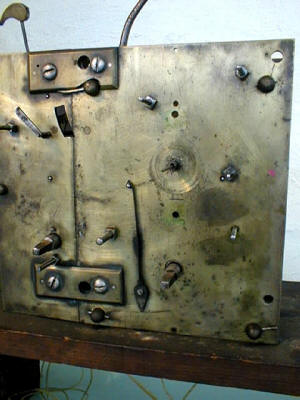 |
This is
the front of the movement with the wheels removed. You can see the two
winding squares - one for the strike (lower left, just above the strap)
and one for the time - lower right. Directly above the time winding
square is the centre seconds shaft poking through. Just visible
surounding the centre seconds shaft is the pipe on which the minute pipe
should run. This has been damaged and will have to be replaced. The
minute pipe is driven via an idler wheel (which is also part of the
motionwork)from the minute wheel, the shaft of which can be seen coming
through the plate to the right of and slightly above the time winding
square. Also visible is the maintaining power clickspring - reaching
upwards from just to the right of the lower strap - but note that the
lever which actually pushes on the click is missing and will have to be
made. |
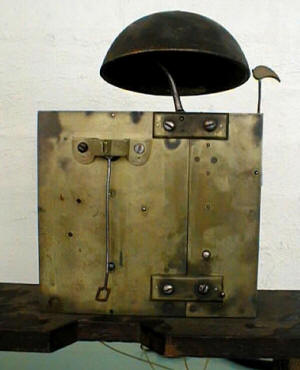 |
This is
the rear of the movement. Clearly seen are the two straps, which
together with the two straps on the front of the movement, secure the
strike mechanism to the time mechanism. The pendulum crutch and hanger
can also be seen. |
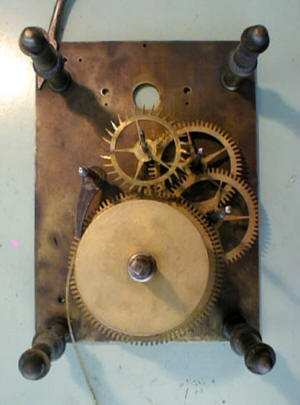 |
This is
the time section of the movement with the front plate removed. The
unusual features to be seen here are:
1) The
layout. The wheel which is normally the 'centre' wheel is moved off to
one side to make way for the escape wheel (carrying the seconds hand) to
be in the centre.
2) The escapement. If you know your escapements, you can see that the
escape wheel is a deadbeat wheel. A clock of this type carrying a large
seconds hand that covers the entire dial would need a much larger weight
to drive it if a recoil escapement was used, due to the larger distance
the large and relatively heavy seconds hand needs to be moved in a
recoil design.
3) The winding system. The maintaining power click is the clue here.
Maintaining power is required to keep the train wheels moving forward
while winding. A deadbeat escapement can be damaged if pushed backwards
while the pendulum is moving |
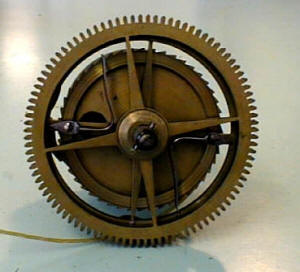 |
Rear
view of the time 'barrel' or 'drum' showing the maintaining power
springs and the spokes (just visible) of the maintaining click wheel.
The design is a fairly direct interpretation of Harrison's maintaining
power design |
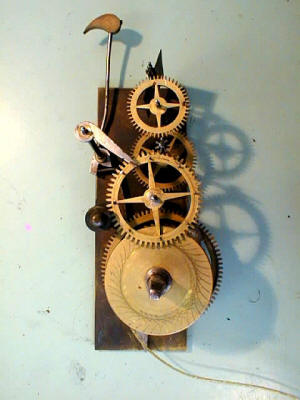 |
The
strike section with the front plate removed. You could be forgiven for
thinking that the strike section had been added by someone other than
the original maker, however the wheels appear to have been made by the
same cutters and the spokes finished in the same way as the time
section. In any case, you would wonder why anyone other than the
original maker would go to so much trouble to provide such a well made
strike mechanism to such a clock as this. |
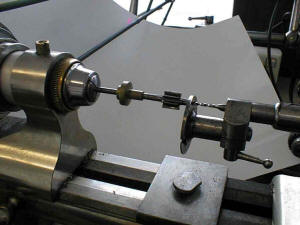 |
One of
the jobs which needed doing was the repivotting of the 'centre' or
escape wheel arbor. This is a picture of the setup for drilling the hole
in the escape wheel arbor to accept the new pivot. The escape wheel has
been removed, as it is held on by screws to the brass collar which can
be seen to the left of the pinion. A tungsten carbide drill is used to
avoid the need to let down the hardness of the arbor |
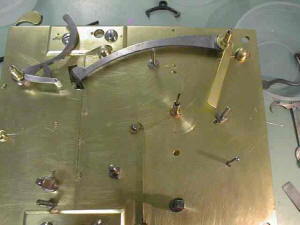 |
This is
a picture of the front plate after cleaning and minor polishing. The
newly made and installed centre (escape) wheel front pivot/minute wheel
rear support pipe and maintaining power ratchet click lever are visible |
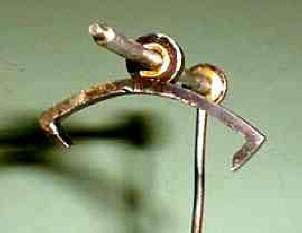 |
The
pallets in the clock had suffered from previous repairers not being
prepared to repair them properly. After almost 200 years, the pallets
were quite worn and clearly someone had tried to fix the wear problems
by bending the pallet arbor, then the arms of the pallets themselves.
The result of the latter you can see here - the left hand side of the
pallets has broken and a new entry pallet has been welded on. While the
clock worked, the pallets were effectively no longer 'deadbeat' and had
turned into recoil. The only course is to make a new set of pallets in
this case |
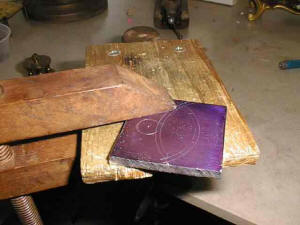 |
To make
a new set of pallets in a workshop that doesn't make pallets every day
requires returning to old fashioned methods, with a few modern twists.
Firstly, the dimensions of the existing parts are drawn up on a CAD
program and the dimensions of the pallets to be made are checked, and
made as close as possible to the original part, at least as far as the
original part has not been damaged or fiddled with. These dimensions are
then transferred to raw material. The scribe marks can be seen in this
picture |
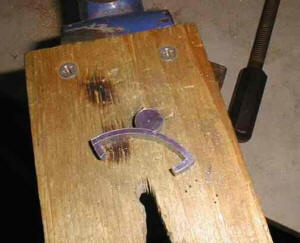 |
After
several hours and many jeweller's saw blades later, the basic shape of
the new pallets is completed, ready for machining on the mill. |
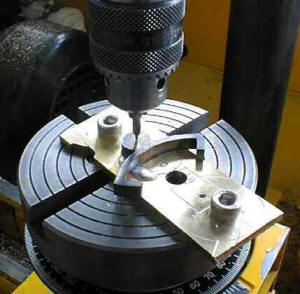 |
The
rough pallets are soldered to a thick piece of brass which serves two
purposes - to enable clamping to the rotary table, and to enable milling
across the entire thickness of the pallets. Plenty of time is spent
ensuring the pallet arbor centre is found, ensuring that the dimensions
of the surfaces of the 'nibs' of the pallets are correct. |
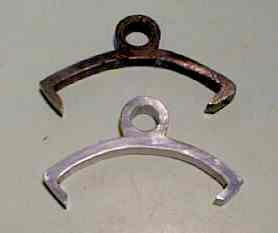 |
After
milling, the new pallets (bottom) look like this, compared to the old
pallets (top). The setup on my mill is not as stable as you would like,
so some final finishing with files and emery papers is required. As you
can see in this picture, the exit pallet (left) is identical to the
original, the entry pallet is as it was when made - remembering that the
entry pallet (right) of the pallets in the clock as bought were broken
off and welded on. |
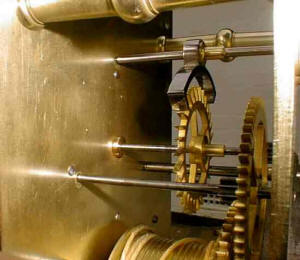 |
After
final filing and polishing, straightening the pallet arbor to return the
pallets to the original dimensions, hardening and polishing, this is how
they look installed in the clock. Compared to the pallets which were in
the clock, the action of the pendulum is about 1&1/2 times the
'original', and is around 10degrees. With an impulse angle of about 1.8
degrees, drop of 0.7 degrees, they are different from the normally
accepted 2 degrees of impulse, 0.5 degrees of drop. These latter figures
are 'normal' for a regulator with an escape wheel in perfect condition.
This escape wheel has had 200 years of wear and is not perfect, so the
new pallets were designed to forgive them |
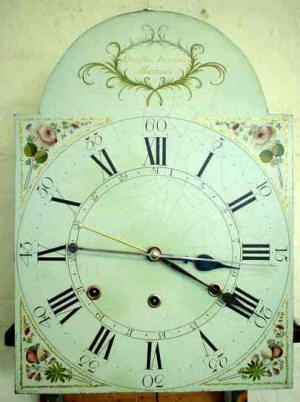 |
This
shows the restored dial, having been cleaned, various chips filled, the
missing date and seconds hands replaced. Note that the seconds hands has
been reproduced from dimensions known from pictures in various
references. Also note that the seconds hand has to be close to perfectly
balanced, or the clock simply won't run. The date hand is made from
brass to make it distinguishable from the other hands. A dial with four
hands on it can be confusing, however with the date made of brass and
the seconds hand moving much faster than the hour and minute hands, the
time is quite clearly indicated on this clock. The sound made by a
centre seconds hand clock is quite different from a normal longcase
clock. As it has been in my workshop for several weeks, I shall miss it
when it is finally shipped to it's new owner - a direct descendant of
the maker living in Florida, USA. |
Thanks to Antique Clock and
Barometer Sales
www.masterclockmaker.com.au |